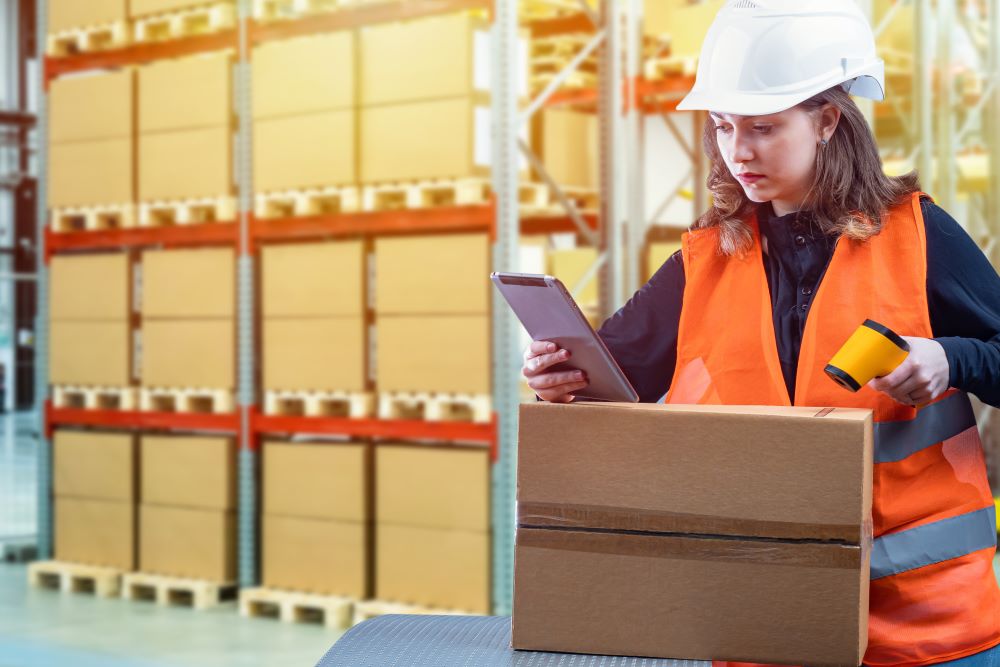
The move from the Customs Handling of Import and Export Freight (CHIEF) system to the new Customs Declaration Service (CDS) has changed how traders make customs declarations. But what risks still exist when making customs declarations, and how can they be dealt with?
We spoke to Customs4trade’s (C4t) director of strategic customer engagements, Ludovic Demeyere, to find out what the risks are, as well as how solutions like self-filing tools can help.
Misconceptions
With the migration from CHIEF to CDS, Demeyere explains, traders are now using “cloud solutions”.
At C4t, he explains, “our CAS platform has been in the cloud from the start, for over nine years now”, and he says that he draws on this experience when discussing the risks associated with customs declarations.
One “misconception” he notes is that, “if a broker does something wrong, then the broker is responsible for the mistake, and this isn’t the case”.
“In the end,” however, he says “in most cases, it is still the customer or the company itself that is responsible for the end result”.
“If there are changes in your supply chain or product, it's essential to communicate all that information to your broker. However, some brokers might simply copy and paste the details to speed up the process, which may lead to errors.
“The main risk that we see with this as a software company is that customers may receive a fine because of the trust they placed in their broker. We’re human, we make mistakes: something that can be avoided by using customs software.”
On managing this risk, he says the first thing to consider is whether or not to “take customs in-house with a self-filing tool”.
“This manages the risks, with a direct connection with customs where the information comes out of their enterprise resource planning (ERP) system.
“We also complete validation checks to make sure everything in a declaration is compliant before sending it to customs.”
As well as taking customs declarations in-house, he emphasises the importance of ensuring the accuracy of the data in your ERP system and seeking the necessary assistance or consultancy.
Pitfalls
When asked about the biggest pitfalls traders should avoid regarding declarations, Demeyere is keen to distinguish between importing through inventory-linked ports and non-inventory-linked ports. He mentions that non-inventory-linked ports, such as Felixstowe and the Eurotunnel, pose significant risks for delays, particularly with fresh foods.
“If you have an import or transit declaration into the UK or a GVMS movement, and the documents are not on time – or the truck gets stopped by customs and you have to go to the broker to get additional information – that can all take hours.
With the Border Target Operating Model (BTOM) also entering force, he notes, new rules on fresh foods, vegetables, seeds and products of animal origin have seen some products face up to 24 hours of delays.
“One of the biggest challenges is that if you have a truck that gets stopped on a Friday evening, your broker may have stopped working at 5pm and then you have to wait until Monday for a resolution.
“One of our customers manufactures frozen potato products and submits approximately 50,000 export declarations each year, with 20,000 of those going to the UK. Since those trucks are loaded with perishable goods, they cannot be delayed at the border for three to four days.”
Solutions
Documentation issues can delay shipments at inventory-linked ports, he adds. If a document isn’t preloaded or released correctly, it can lead to complications.
Demeyere explains that, by managing this process in-house, Inventory Reference Numbers (UCNs) can be “auto-claimed”. This allows customers to upload their data, have it preloaded at the port, and automatically release the preloaded documentation.
This automated approach reduces reliance on carriers, Demeyere says, which “can cause some delays too”.
Customs4trade provided this insight as part of its supplier membership with the Chartered Institute. Find out more about the supplier membership offer here.